Seven Design for X concentrations that create Business Value
Design for X explores multiple solutions to problems, boosts team collaboration, and drives your mission forward at a steady pace.
While there are many possible values for X, the seven most common points of focus involve manufacturability, testability, reliability, safety, serviceability, cost, and compliance - areas that can be defined, most often due to an issue that has arisen in a product.
What is Design for X?
Design for X (DFX) is an approach to engineering and design that focuses on a primary variable of a product or process, and narrows in on the design activities that will influence that trait or feature as the desired outcome of a project. If a company is looking to improve a product in the face of new competition or a market shift, extend the lifecycle (and profits) of an existing product who's components are harder to come by, or to quickly solve a new performance or compliance issue that has arisen, the focus of DFX can be a powerful tool.
How Product Development Experience Supports DFX
DFX is a tool that helps to understand the power of design in outcomes. But too narrow of a focus could result in multiple design iterations and unforeseen design conflicts within a company's products. It's important to focus on the objectives of your DFX, while also keeping broader design principles in mind.
Understanding of DFX principles within the larger context of product design and development will help you reach your objectives without creating additional issues. Working within a development framework while targeting your variable ensures a focus on objectives, and the outcomes you plan for. Do not use DFX as a way to sidestep known product development steps, such as specification development, product validation testing, risk evaluation, and other considerations. DFX must be practiced inside of the larger product development framework.
Seven Common focus areas of DFX that create real value
- Manufacturability: Innovative Solutions and the commercialization of a great idea are concepts that can often run at odds with each other. Many organizations are driven with a passion to solve problems, but lack experience to turn the solution into a profitable product and a sustainable business. Design for Manufacturability (DFM) as a discipline enters the product development process when the focus shifts from solution to production, or from the focus on performance to the focus on repeatability.
One aspect of repeatability in manufacturing is the availability of parts. At some point in a product lifecycle, components that were once readily available may be phased out from a supplier. In this case, production can be slowed, halted, or discontinued if a replacement is not found. DFM can be applied to evaluate the impact of the change and design a solution to bring manufacturing back to levels that sustain target returns. Learn how one tool manufacturer designed in replacement electronics and also improved performance and usability.
- Testability: Often a product can be selected for usage by a customer that includes a requirement for more rigorous testing beyond what was originally designed. It's not uncommon for commercial products to be selected for use in aerospace or medical products, markets that require added levels of reliability and conformation testing before acceptance. Design for Testability (DFT) helps re-evaluate existing designs and adjust engineered aspects to accommodate the need for additional or alternate testing techniques or outcomes. Read how one medical diagnostic company used existing technology to break into the at home testing market.
- Reliability: A great design and an initial production system doesn't always mean immediate and lasting success. Often times companies find themselves needing to update, improve, and redesign their first concepts, tooling, inspection systems, or other production aspects based on feedback from the users in the field. Reliability of design, or more importantly a lack thereof, can turn a great concept into a commercial flop if the product doesn't perform reliably. This becomes even more pressing when the result is the failure of a product already launched into production.
Design for Reliability (DFR) takes the components of an unreliable solution and salvages the good aspects of design, incorporating updates to eliminate the failures causing issues. By using the reliability framework, product companies can focus on the causes of the reliability issues, make calculated and focused redesigns, and re-launch their product for market success. See how one snowboard innovator sharpened its competitive edge with redesigns. - Safety: While innovative solutions may exist for solving problems in harmful environments, the focus on keeping humans out of harms way will continue for all product or service innovators. Design for Safety (DFS) places a level of importance in the safety considerations of individuals using a product or in proximity to products being used. By emphasizing safety as the primary design outcome, engineers develop solutions that further that aim of protecting health and wellness. Robotics is an area where design is applied to keep humans out of harm's way.
- Serviceability: Related to reliability, designing your product for serviceability can create a competitive advantage in markets where maintenance and upkeep are a integral aspect of product performance. Leveraging the relationship between product up-time, service intervals, and customer profit performance will give any company the edge they need in a competitive marketplace. Design for Serviceability (DFS) provides the framework for understanding how to compete in areas that aren't as direct as many may think. Augmented reality technologies are improving turn around times for in field repairs while also reducing training costs.
- Cost: Always a driver of change regardless of market, reducing cost is a powerful tool for sustaining profitability and extending the lifecycle of existing designs. Newer technologies and solutions will continue to disrupt the marketplace, but companies can take advantage of Design for Cost (DFC) to get returns from current product iterations while developing their longer-term response to new competition.
Similar to Design for Manufacturing, a review of existing components, processes, testing, and available technologies can reinvigorate a current design and provide cost reductions across the product, sustaining profitability for a foreseeable period of time. Review of cost savings can reach outside of just components: often a simple evaluation of available features, vendor processes, or other peripheral considerations can yield results. Read about a national fast-casual restaurant chain that required its cooking system manufacturers to reduce costs while enhancing features. - Compliance: Designing products to be used in heavily regulated markets is a skill set that has to be developed over time. Medical Devices are a typical product set that requires a deep understanding of how to bring the performance, results, and compliance of a product together at the right time. Design for Compliance (DFC) principles are best applied from the project initiation, and development should begin with compliance milestones at the forefront of consideration. Read about utilizing product development best practices in medical device product development.
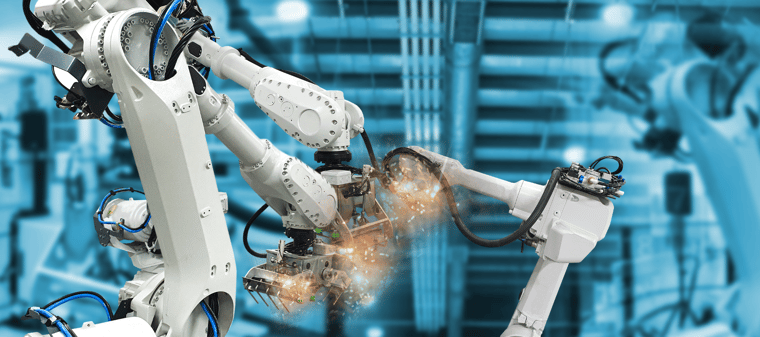
Impossible Challenge? Try Us.
Selecting a partner to help you complete your design project is a valuable option to reduce project duration and save money.
The Boston Engineering product development system encompasses DFX to ensure a smooth product launch and success in the marketplace. Boston Engineering has DFX knowledge and experience to address aspects and values of a product such as manufacturability, test, reliability, safety, serviceability, cost, and compliance with industry standards and government regulations.
A focus on your product. Manufacturability is embedded throughout our product development process to achieve cost, feature, and performance requirements. Our product development plans target your manufacturing, cost, timeline, reliability and supply chain needs, as well as other critical requirements.
Our primary DFX capabilities include:
- Design for Manufacturability (DFM)
- Design for Assembly (DFA)
- Design for Cost (DFC)
- Design for Testability (DFT)
- Design for Reliability (DFR)
- Design for Serviceability/Maintainability (DFS)
- Design for Usability (DFU)
- Design for Modularity (and Product Platform Design)
Don't see your requirement here? Try Us! We can engineer what many others can only imagine.
Imagine your Impact: Stay up-to date- with the latest insights and trends we're watching. Add your email address below and sign up for a Monthly Summary of our most impactful posts!
